聚焦 智慧梁场 以智提效 新格局 探渝昆铁路 新升级开创
发布时间:2024-10-10 00:46:07点击:
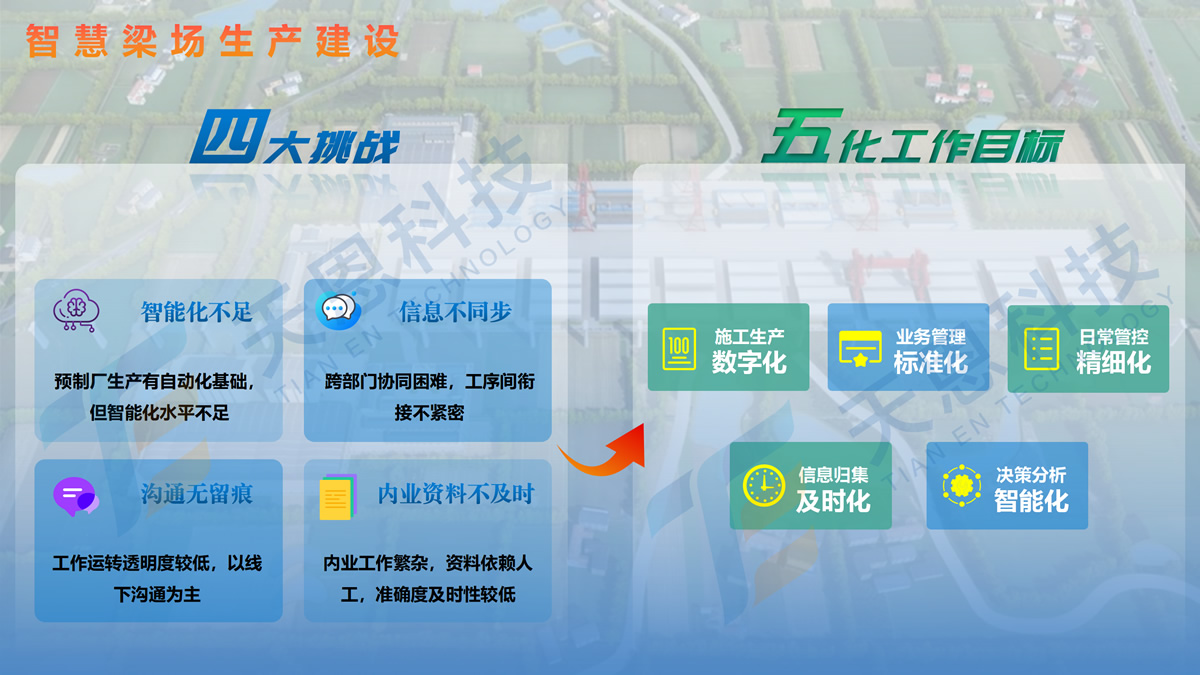
在渝昆高铁五标宜宾东制梁场,一群特殊的“高铁建设者”正奋战在各条生产线上。
“这是我们梁场的主力工人——智能机器人。”梁场的人介绍说,这里的“智能机器人”代替了三分之二的工人,同时工作效率是传统加工设备的两至三倍。
通过全封闭智能化梁场的建设,铁路制梁现场井然有序、有条不紊;作业人员各负其责,弯筋、剪切、绑扎、预制、注浆、养护……
人拉肩扛的铁路建设已经成为过去式,“无人”工厂、流程化生产的模式正在走进高铁建设工地。伴随着中国铁路建设技术、质量的飞速提升,新建渝昆铁路重庆至宜宾段站前工程YKCYZQ-5标项目部怀揣着对高铁事业、技术创新的孜孜追求,不囿于现状,不拘于传统,将基于BIM技术与智能化技术的铁路标准箱梁设计与制造作为发展的目标,奋力打通设计与施工之间的信息壁垒,致力将渝昆五标宜宾东制梁场打造为提质增效的“智”造利器。
渝昆高铁,全长699公里,是我国“八纵八横”高铁网北京-重庆-昆明铁路大通道的组成部分。中铁三局担负着渝昆高铁宜宾段全长37.7公里的施工重任。由于受到自然地形等因素影响,桥梁占工程比例高达61.8%。
预制梁场,作为桥梁标准化建造与施工的重要基地,其规范布置与合理规划,对工程进度和成本控制起着至关重要的作用。而宜宾东制梁场,主要承担渝昆铁路站前五标范围内双线桥41座、共计511孔双线简支箱梁预制。然而随着项目进程的推进,传统工装技术的落后,给梁场施工带来的问题尤为突出。使生产质量得稳定性难以掌控,同时也造成了大量的资源浪费;设备自动化程度低,施工现场“人挤人”交叉干扰;人工参与度过高,导致熟练工种难以为继,也使成本持续增加;传统设备故障高,利用效率较低。
中铁三局渝昆项目部以“三大转变”为指导,坚持守正创新,为解决宜宾东制梁场施工过程中的痛点、难点问题,构架工装研发“一擎两翼”新途径,全面提升梁场的施工生产能力、管理水平和创新能力,全力打造渝昆铁路制梁标杆—智能化品质梁场。
智能终端:“最强大脑”
针对传统制梁暴露出的诸多问题,宜宾东制梁场在管理模式和产品生产线上进行了“改头换面”和“迭代升级”。通过智能化控制中心的梁场管理系统、三维空间数字化模型、语音发布系统,现在的调度管理只需1人在智控中心,5分钟就能完成现场监督、上传下达。
为实现机械化换人、自动化减人、智能化管控的目标,项目部研发了适合铁路标准化梁场管理体系的信息化系统。系统全面涵盖梁场施工的物资管理、设备管理、生产全过程管理、进度管理、安全质量管理、工程试验智能管理,以BIM技术为核心,发展物联网+箱梁智能建造新模式,依托5G技术、物联网、智能机器人、激光定位等高精尖技术建立贯穿全生命周期的全过程控制和管理的铁路梁场综合管理标准化系统。
项目部还将自动张拉、自动压浆、自动静载、自动喷淋等相关数据集中于“一个系统”,充分利用数据集成和数据共享功能,自动生成检验记录、报告和制造技术证明书等,有效消除“信息碎片”和“信息孤岛”带来的难题,实现原始资料一次录入、多处复用,减少重复录入工作,将最终数据直接归档及交接给运营管理单位,为梁场生产管理提供智能化的辅助决策,实现了预制梁生产过程中原材料数据的自动采集、统计、分析及预警,实现数据无纸化记录、全过程管理。
目前,智能终端,已成为辅助项目各级管理者管理“智慧梁场”的“左膀右臂”,是实现宜宾东制梁场标准化管理、智能化管控的“助力器”。
智能工装:集“智”创新
智慧梁场并非简单的形式表现,而是融入多种智慧创新的新型智慧梁场。
“在制梁技术日趋成熟的今天,单从技术上突破已经很难,只有从工序中发现新亮点,通过巧干活提质增效。”渝昆铁路五标项目部以独特的思维,手把着这把创新和增效的“金钥匙”。
设备更新是解放劳动力、降低人工成本最有效的途径,项目锚定高质量发展,以现代化工程管理为抓手,在“智慧梁场”的钢筋工程、模板工程、预应力工程、混凝土工程、成品检测工程的生产线上进行多维度全面升级,通过设备的改进创新,为施工安全质量保驾护航。
秉持“展示亮点、研究超前、投入适中、产权自主”的主导思想,项目于“智慧梁场”投入使用钢筋自动加工生产线,包含数控钢筋剪切生产线、数控立式钢筋弯曲中心、数控斜式钢筋弯曲中心、数控钢筋调直弯箍机,可实现梁体钢筋的自动加工,配合AGV无人运输车的使用,可实现成品料运输、存放;并由定位焊接机器人,完成定位网的物料焊接与存放;以数控弯箍机配合智能机械手臂,完成联系筋、三墙钢筋的加工、自动抓取摆放。
梁场技术人员说,目前钢筋加工已实现“少人化”生产模式,降低约85%的人工投入。通过采用自动化的工艺流程,有效实现高精度钢材加工、“零”污染焊接施工的“智慧梁场”发展目标。
在施工人员上做“减法”,在施工效率上做“加法“,是项目建设智慧梁场的初衷。宜宾智慧梁场建设过程中,模板工程生产线同步升级,内外模各采用自动打磨设备与纵横移动形式,借助全自动汽车清理原理,完成内模和外模打磨、灰渣吸尘及脱模剂喷涂一套流程全自动化无人操作,单套模板用时仅35分钟,有效避免传统施工的机械伤害,确保模板各个部位无遗漏打磨、脱模剂均匀喷涂,减少积液情况发生。在钢绞线切割、锚穴凿毛和梁端防水层施工过程中,梁场采用钢绞线切割凿毛台车,有效节约人工成本、降低安全风险。
他们始终坚持“以智增效”的原则,为解决预应力箱梁养护费工费时的难题,“智慧梁场”采用全自动智能喷淋系统,箱梁顶板采用蓄水养护,侧面、底面及箱内采用温湿度智能控制喷淋养护设备,避免由于人为因素出现不养护、漏养护的问题。
为实现“以工装保工艺、以工艺保质量、以质量保安全”的管理目标,梁场采用桥面自动振捣设备、辅以桥面激光整平机,切实做到桥面振捣频率和振捣深度可控,将梁面整平精度控制在±3mm以内,有效避免箱梁桥面施工出现漏振、过振情况,助力智慧梁场实现高标准、品质化升级。
在每天两孔的生产进度下,智能工装的研发及应用可以在原来128人的基础上减少80人,提高至少1.3倍的施工效率;在钢筋、模型、养护、张拉、压浆、防水等传统作业上,可以有效节约13小时,通过智能化设备的应用为项目建设提质增效。
本文关键词:
本文为文章出自:互联网,文中内容和观点不代表本网站立场,如有侵权,请您告知,我们将及时处理。
: 闵廷超赴厦门新会展装饰项目检查 : 渝昆临电35kV黄草开关站一次送电